By Mary Koutras, Technical Leader
Lean Culture embodies a variety of principles and ideals. Most recognize Lean as being an automotive practice as it was developed to assist with manufacturing production by identifying and eliminating waste, thus increasing throughput. Although Lean Manufacturing was developed in automotive, the reality is any cyclical process or business can benefit from the methodology of Lean by evaluating non-value-add activities. For example, one of the ways that Duro-Last eliminates waste from your processes and aids in Lean practices in the field is by offering custom-fabricated deck sheets. As the consumer, you receive consistent, quality welds, and the deck sheets can even be labeled and designed for ease of installation layout. This ultimately eliminates wasted time for your rooftop crews, meaning you can move on to the next project quicker and spend less time and resources on non-value-add activities.
In the upcoming continuous improvement articles, we’ll go through a few of the eight wastes, Lean principles, and how they apply to you. This article in particular will cover the visual workplace organizational system known as 5S.
Have you ever misplaced tools or equipment, resulting in wasted time and frustration? The 5S concept was developed to address just that, and stands for: Sort, Set, Shine, Standardize, and Sustain.
To start with the 5S program, Sort through all of your existing tools, equipment, and inventory. Ask yourself, “What is the item use, how often do I use it, and does it need to be here?” Eliminate things that are no longer necessary.
Next, Set-in-Order – every item should have a proper location. For example, copy paper should be located near the printer. Use shadow boards, floor markings, color coding, and labeling as a visual indication to determine if everything is in the proper location.
Shine and clean all workspaces and perform regular maintenance to prevent breakdowns.
Standardize and identify a way to maintain the work areas, equipment bags, etc., by posting checklists, cleaning schedules, or charts.
Lastly, Sustain the program. Sustaining the program through training, accountability, and diligence is the hardest of the 5S principles to maintain. The intention is to make 5S a long-time commitment, not a yearly activity.
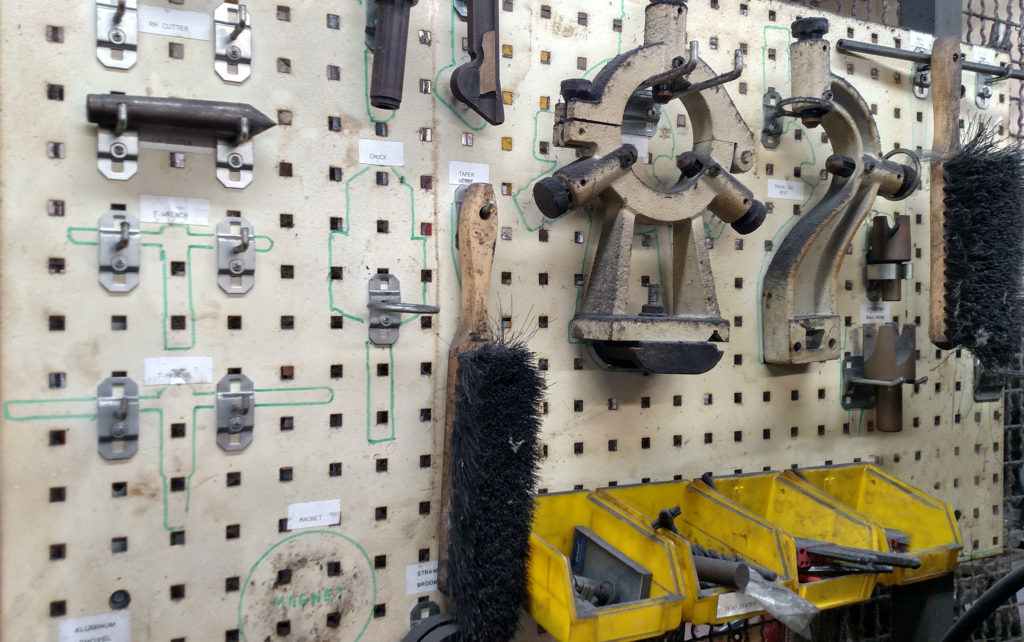