By: Roseann George, Director of Procurement
Lumber supplies in the U.S. are facing a shortage as a result of the coronavirus pandemic, presenting issues for the housing and construction market.
Several major lumber mills cut back on their production when COVID-19 arrived in the U.S. earlier this year due to widespread lockdown orders and a forecasted downturn in demand. Mill officials had concerns of a worsening economy and the health and safety of their employees, but didn’t foresee demand rebounding as quickly as it did.
Over the past 6 months, quarantines enacted throughout the country caused a spike in do-it-yourself projects with Americans heading in droves to their local home improvement store to purchase construction supplies. Lumber producers didn’t anticipate the resurgence of the housing sector being as strong as it has been and the massive increase in do-it-yourself demand.
In some cases, lumber prices have doubled and tripled over the past year. OSB board prices, for example, were three times higher in September 2020 compared to September 2019. Other prices have gone way up, too. Western SPF (spruce, pine, and fir) 2x4s, for example, have gone up 158% over the past year, studs have risen 164%, and southern pine has gone up 147%.
Housing starts, which dropped 40% between February and April, returned in July to their prepandemic level of about 1.5 million on a seasonally adjusted annual rate. Builders and consumers are having an easier time finding lumber, but they are paying dearly for it.
The NAHB (National Association of Home Builders) recently posted an article speaking to how this rally has impacted the cost of home-building: “Since mid-April 2020, lumber costs for the average single-family home have climbed more than 130%. According to the NAHB analysis, this has resulted in an increase of more than $16,000 in the price of a new single-family home.
The LBM (Lumber/Building Material) organization conducted a survey of 442 dealers regarding material shortages. Two key area responses are listed below.
1. Is your company able to source all the lumber and building materials your customers require?
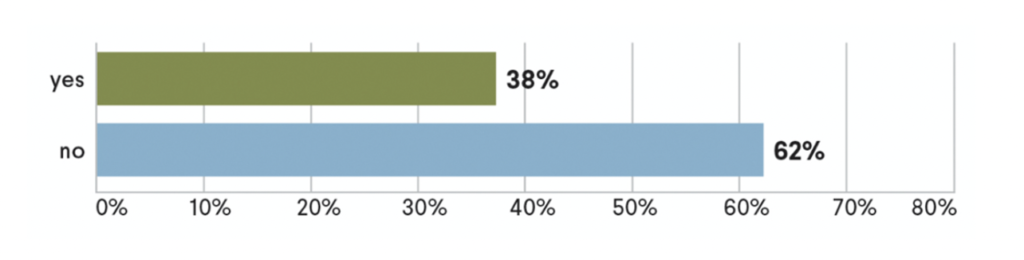
In the graph above, 62% of respondents were unable to find all the lumber and building materials their customers required.
2. Which products are you having trouble getting from your vendors?
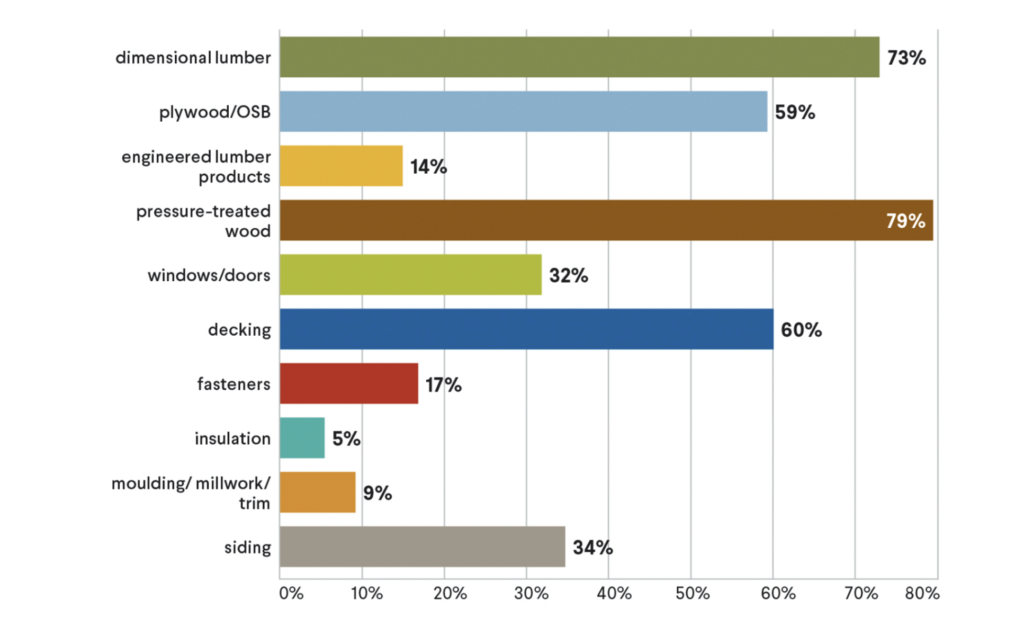
Charts Source: LBM Journal Oct 2020
Pressure treated wood is the most sought-after material. According to the survey, nearly 80% of dealers are experiencing trouble sourcing these materials. Dimensional lumber isn’t far behind, as 73% of dealers indicated difficulties obtaining what their customers require. Plywood/OSB and decking also make up significant shortages, with around 60% of respondents indicating shortages of these materials.
Now that COVID-19 is here to stay, things have become much more unpredictable. In order for prices to come down, several things need to happen. In the U.S., lumber production will need to increase, shutdowns within the lumber industry will need to come to an end, and timber producers will need to increase the amount they’re producing in order to bring costs down.
Once these things start to happen, lumber prices should fall, but when that may happen depends on when life will return to “normal,” and no one knows when that might happen or how quickly lumber prices may fall when it does happen.
What goes up, must come down and as this unprecedented rally runs its course, undoubtedly there will be more hurdles to overcome.