By: Don Garno, Custom-Fabrication Product Manager
Custom-cut Duro-Last X (DLX) membrane, combined with our Duro-Bond® induction welding system, can save you significant labor hours due to less field seams, less T-Patches, and less material handling on the job. As demonstrated in the drawings below, DLX can essentially eliminate the use of T-Patches that are required when installing a standard length roll good system. For example, on a roof that is 123 feet wide (as in the diagrams below), a standard roll would typically only cover 100 feet before you ran out of material. Meaning you would have to start a new roll to complete the full width of the building before moving on to the next section. Then when you start rolling out the next section of roof, you’d only have a partial roll left from what was used on the previous section. And with each new membrane roll you start, T-Patches are required, adding an additional step to the installation. By contrast, the DLX membrane can be cut to the exact width of the roof (up to 200 feet). No need to start a new roll halfway through the section, and no need for T-Patches.
Believe it or not, that’s just one level of efficiency provided by the DLX membrane. Couple custom-lengths with induction welding technology, and field-seams are further reduced by eliminating the need to “picture frame” the perimeter of the roof for additional fastening security. In the example below, you would simply order 10-foot DLX membrane, custom cut to 123 feet long, and enhance the perimeter as needed with additional induction plates. No T-Patches, no end-to-end welds, no unusable scrap or “butt” rolls to remove. In the end, it allows your roofing crews to get the installation done faster and on the next job sooner.
Visit www.duro-last.com/duro-last_x to learn more about the features and benefits of the DLX membrane, and contact us today if you’re ready to explore how Duro-Last’s custom capabilities can enhance rooftop efficiencies on your upcoming roofing projects!
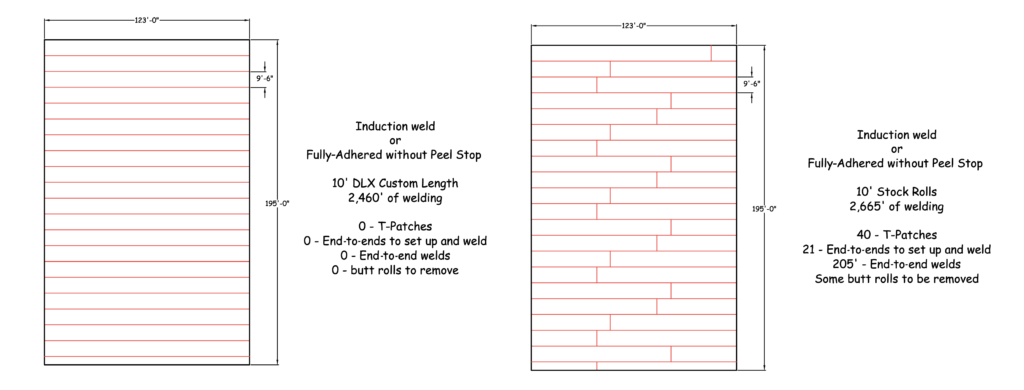